Can your HVAC system pass the efficiency test? This is why it most likely can’t
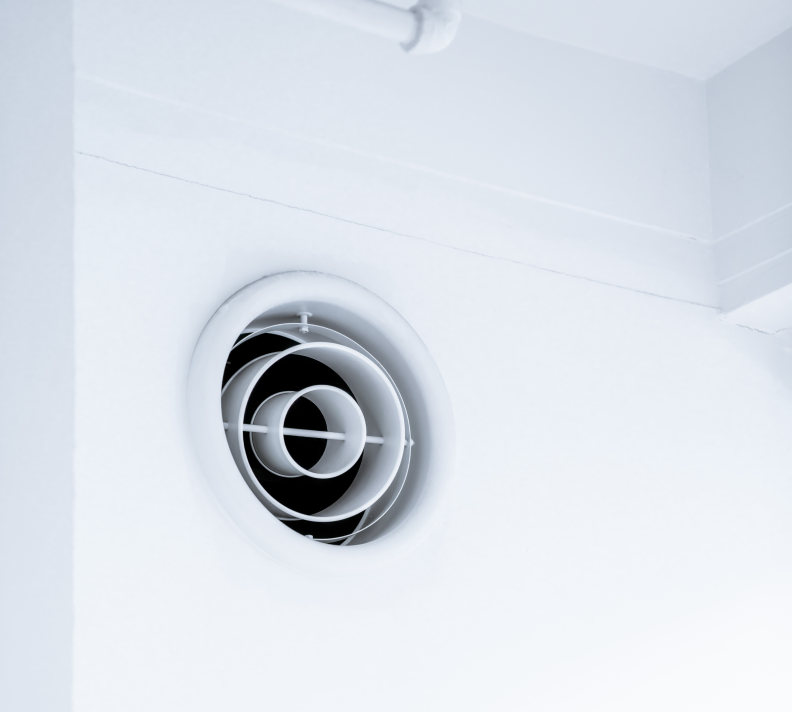
HVAC systems represent the largest share of energy consumption in commercial buildings. Space heating is a larger load for buildings in cold climates, while air conditioning is a larger load in warm climates. However, HVAC systems as a whole normally use more energy than any other system.
In 2016, the New York City Urban Green Council analyzed energy consumption data for over 10,000 properties, including both residential and commercial buildings. They found that HVAC systems represent 44% of energy consumption overall: 49% in multifamily residential buildings, and 45% in commercial buildings.
Many HVAC systems provide excessive heating, cooling, or ventilation, which means they don’t operate at peak performance, thus wasting energy and money. The following are some common causes of energy waste in HVAC installations:
- Using HVAC systems that follow older design standards, such as previous versions of ASHRAE 62.1 that mandate a minimum outdoor airflow. This increases both heating and cooling needs, since airflow cannot be reduced below the minimum value.
- Building envelope issues, such as air leakage and poorly insulated areas. Low insulation and air leaks cause heat gain during summer and heat loss during winter.
- Using HVAC equipment that was sized based on “rules of thumb”, instead of a professional design. This often leads to oversized installations, which use more energy. For example, some air conditioners are sized based on square footage only, without considering the number of occupants or the intended usage of the conditioned area.
- Having equipment controls with an incorrect configuration that causes excessive heating, cooling or ventilation. A situation that can be turned around without carrying out any renovations.
If your HVAC system is consuming more energy than necessary, it is likely due to the causes above, alone or in combination.
In this article we are going to look into each of the above causes and propose solutions that can be implemented to improve the efficiency of HVAC systems.

How Older Design Standards Increase HVAC Expenses
The 1979 version of the ASHRAE 62.1 standard introduced the Indoor Air Quality Procedure (IAQP). This procedure allows the design of ventilation systems to control air pollutants directly, without having to meet a minimum airflow value. This optimizes the workload on space heating and air conditioning units, since they handle just the right amount of air.
However, many building codes still use the older method based on floor area and occupancy, called the Ventilation Rate Procedure (VRP). The VRP requires a minimum airflow at all times, even when indoor air quality is good, and this limits the opportunity to save energy.
- Countries and municipalities develop their building codes according to internationally recognized standards, such as ASHRAE 62.1.
- Since the Indoor Air Quality Procedure does not have widespread adoption yet, there are still many places where the Ventilation Rate Procedure is mandatory.
- The IAQP represents an excellent chance to save energy, once it has been adopted by local building codes.
- Even when the VRP is mandatory, a hybrid design is possible to control air pollution more effectively.
There might be different reasons why authorities have not adopted the IAQP version yet. The VRP is based on hard data: airflow rates suggested by ASHRAE. On the other hand, the IAQP basically says “determine your own air pollutants and their maximum acceptable level”. Thus local authorities will prefer the method that uses hard data when creating their building codes as it’s easier to control and enforce even though it has major disadvantages in terms of efficiency and air quality control.
The VRP from ASHRAE follows an indirect approach to calculate the ventilation requirements of an indoor space. Instead of providing design guidelines to control air pollutants directly, ventilation systems have been sized based on three factors:
- The occupancy classification or intended purpose of the indoor area.
- The total floor area.
- The number of occupants.
Air pollution is influenced by these three variables, but the indirect design approach of the VRP has a major disadvantage. Since air pollution is not controlled directly, there are times when the building is under-ventilated or over-ventilated. Insufficient ventilation is detrimental for air quality, while surplus ventilation represents a waste of energy. Surplus ventilation also increases the workload and energy expenses of heating and cooling systems, since they must handle more unconditioned outdoor air. This scenario improves with the introduction of demand-controlled ventilation.

A DCV HVAC system automatically reduces airflow in unoccupied spaces.
Demand-controlled ventilation (DCV) consists on reducing airflow when the full output of the ventilation system is not needed. For example, an office needs less ventilation if most of the staff is away attending meetings with clients.
- The energy savings from DCV have a lower limit when HVAC systems are designed with the Ventilation Rate Procedure, since there is a minimum airflow to keep.
- On the other hand, the Indoor Air Quality Procedure can achieve synergy with a DCV system, since the lower limit disappears.
The Ventilation Rate Procedure has dominated HVAC designs globally, and traditional DCV systems respond to occupancy variations, while staying above the minimum airflow value. These DCV systems have a limited ability to control air quality, since they cannot respond directly to air pollution levels.
By using an accurate air quality monitoring system like Foobot Smart Air Building, a DCV system can respond directly to air pollutant concentrations. This provides improved control over air quality, compared with a system that only responds to occupancy. A smart control system like Foobot’s also saves energy by preventing overventilation, overheating and overcooling, something a VRP system fails to achieve by design due to the minimum airflow required by older standards.
Importance of the Building Envelope
Even if you have an efficient HVAC design with air quality monitoring capabilities, there may still be energy waste if the building envelope has a poor performance. Ideally, the building envelope should minimize heat transfer between the building interior and exterior, in both directions. To achieve this, there are two important requirements:
- The building must be properly insulated to minimize heat conduction across walls, floor slabs and rooftops. Energy efficient windows also improve insulation, especially if they have triple-pane glass and low emissivity coating.
- The building must also have an airtight construction, since losing conditioned air from indoor spaces is also a waste of energy.
Having the Right Equipment Capacity and Configuration
Oversized equipment and incorrect control settings can also cause energy waste in HVAC systems. Oversized equipment is common in older installations, which were often sized based on “rules of thumb”. Thanks to modern tools such as energy modeling software, equipment capacities can be calculated much more accurately in new projects.
Energy modeling is a powerful tool, but its results depend on the input data and the methods used. Currently, the Parametric Analysis Tool (PAT) is one of the most accurate methods available. It was developed by the National Renewable Energy Laboratory (NREL) and the Oak Ridge National Laboratory (ORNL), which are both funded by the US Department of Energy. Foobot algorithms have been used successfully for energy modeling with 25.9% more accuracy than the NREL/ORNL benchmark.
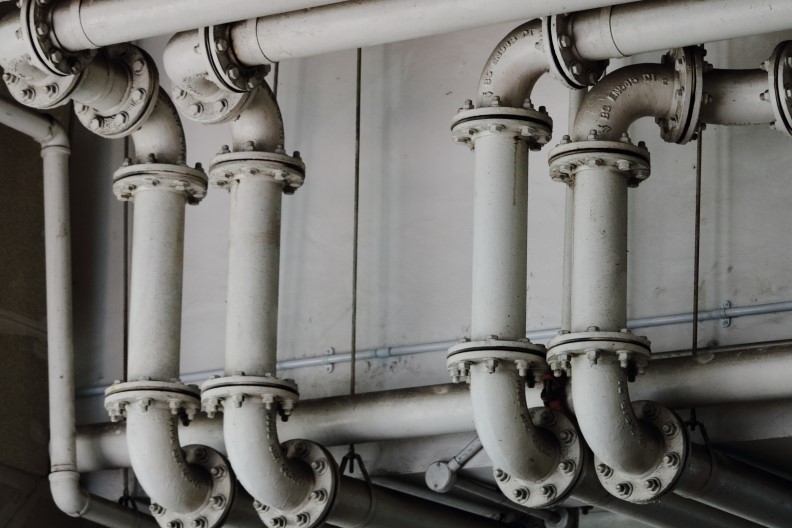
Old building codes required enough heating capacity to make up for open windows.
In some cases, oversized equipment is also a consequence of older design standards. For example, oversized heating systems are common in old buildings, since building codes from several decades ago required enough heating capacity for buildings with open windows. On the other hand, modern building designs focus on airtightness to improve energy efficiency, and these old heating systems are oversized according to current design practices.
An HVAC system of inadequate capacity may also suffer from poor control over temperature and humidity. This is detrimental for comfort, and lack of humidity control also has a negative effect on air quality.
Comparing HVAC Control Options: Rule-Based Controls and AI
The typical way of managing HVAC systems is via rules with a so-called rule-based control system.
The Ventilation Rate Procedure (VRP) is based on minimum airflow rules, and a ventilation system designed with this method is bound to the same rules. Airflow can be decreased based on occupancy, but it can never drop below the minimum value as calculated according to ASHRAE 62.1. Most VRP systems are managed by rule-based controllers.
On the other hand, the Indoor Air Quality Procedure (IAQP) is not limited by a minimum airflow, which gives greater flexibility when programming the control system, and hence providing better efficiencies. This procedure requires a smarter controlling system, such as AI, since it needs to measure and respond to indoor air pollution, besides all the other HVAC parameters.
The indirect design approach of the VRP has a major disadvantage compared to the IAQP. Since air pollution is not controlled directly, there are times when the building is under-ventilated or over-ventilated, and so wasting energy.
Foobot simulated energy consumption with rule-based controls and AI-based controls for a “medium office”, as defined by the US Department of Energy:
- 53,600 sq.ft.
- 3 floors
- 33% window fraction
- Office building
- The energy sources are electricity and gas
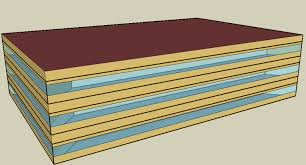
When HVAC energy consumption was simulated for an entire year, the rule-based control resulted in 1439.60 gigajoules, while the Foobot’s AI control decreased consumption to 1169.48 GJ. This represents 18.8% in energy savings. When moving from a desirable temperature range to a thermal comfort zone according to ASHRAE 55, Foobot’s technology achieved energy savings of 38%.
Let’s translate these savings into dollars.
According to a 2016 study by the NYC Urban Green Council, a typical office building uses 19% of its energy for space heating, 13% for space cooling, and 13% for ventilation. The energy source for space cooling and ventilation is electricity, while space heating systems typically use natural gas or another fossil fuel. Based on the energy use breakdown from the NYC Urban Green Council, the HVAC systems in our example would have the following consumption before and after applying AI controls:
HVAC sub-system | Energy Consumption with Rule-Based Control | Energy Consumption with AI-Based Control | Energy Savings |
Space Heating | 607.83 GJ | 493.78 GJ | 114.05 GJ |
Air Conditioning | 415.88 GJ | 337.85 GJ | 78.03 GJ |
Ventilation | 415.88 GJ | 337.85 GJ | 78.03 GJ |
To get an idea of the potential energy savings, the heating energy can be converted to thousand-cubic-feet of natural gas (MCF), while the air conditioning and ventilation energy is converted to kilowatt-hours.
- 1 GJ = 277.7778 kWh
- 1 GJ = 0.9478 MCF of natural gas
By applying these conversion factors, the following results are obtained:
- Total electricity savings = 78.03 GJ + 78.03 GJ = 156.06 GJ
- Electricity savings in kWh = 156.06 GJ x 277.7778 kWh per GJ = 43,350 kWh
- Natural gas savings in MCF = 114.05 GJ x 0.9478 MCF per GJ = 108 MCF
The estimated electricity savings are 43,350 kWh, and natural gas savings are 108 MCF. In the latest data reported by the US Energy Information Administration (September 2019), natural gas has an average cost of US$8.33 per MCF in commercial buildings, while electricity has an average cost of 10.97 cents/kWh. The following table presents the heating savings in MCF of natural gas and US dollars, while air conditioning and heating savings are provided in kWh and US dollars:
HVAC sub-system | Energy Savings | Cash Savings |
Space heating | 108 MCF | $899.64 |
Air conditioning and ventilation | 43,350 kWh | $4,755.50 |
In this example, the annual energy costs of the building are decreased by $5,655.14 only by using a smart HVAC control instead of a rule-based one. These energy savings could go up to $11,430.6 by moving from a desirable temperature range to a thermal comfort zone as previously mentioned. It’s important to note that these savings are achievable without spending a dime on renovations.
Conclusion
Many HVAC systems waste energy, and this can be caused by several factors. Some installations follow older building codes, which provide less flexibility to optimize airflow, heating and cooling. Energy waste can also be caused by oversized equipment, or using rule-based controls instead of smart controls.
In general, an HVAC system wastes energy when there is overventilation, overheating or overcooling. Deficient building insulation and air leakage also waste energy by increasing the workload on HVAC systems, even when they are designed and controlled optimally.
When HVAC systems are controlled with a smart air quality monitoring system like Foobot Smart Air Building, they can respond directly to air pollution levels, while optimizing the workload on fans, air conditioners and space heaters.
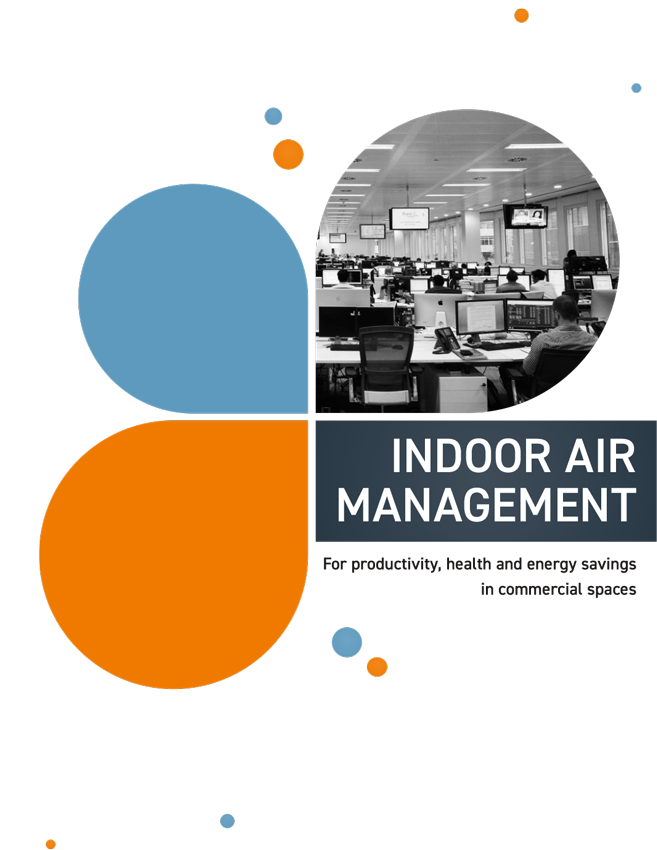
Indoor comfort and energy savings on autopilot
Thermal comfort and indoor air quality are very correlated to staff health and cognitive performance, studies say.
Since human resources are businesses’ largest expense, it’s time to give them the best.